Variable Frequency Drive Frequency Given Mode
Variable frequency drive output frequency is controlled by frequency given signal, the so-called VFD frequency given mode refers to specific methods controlling the VFD output frequency. Common variable frequency drive frequency given modes include:
Panel Given Mode
It means to complete frequency given through the keyboard or potentiometer on the VFD operation panel. The VFD output frequency can be setting through up and down keys on the panel keyboard. Some VFDs are also equipped with a potentiometer, which can be rotated to set the frequency. Such a setting mode is suitable for local operation, which is convenient and easy, but it’s unable to transmit in a long distance.
External Given Mode
In this mode, the frequency given signal is input from the external terminal of VFD to control the output frequency. Common modes include:
1. Analog signal setting
It means to connect DC voltage or current signal from the VFD control terminal to complete frequency given, namely adjusting the VFD output frequency by changing the signal through dcs system, plc, PID regulator and manual operator. Commonly used voltage signals include: 0-10V, 2-10V, 0-±10V, 0-5V, 1-5V, 0-±5V. Current signals include: 0-20mA, 4-20mA. Current signal should be preferentially selected for this kind of signal because current signal has a long transmission distance and strong capacity of resisting disturbance. If the transmission distance is not long, the voltage signal can be selected.
2. Digital signal setting
It means to complete frequency given by inputting on and off signals through the VFD control terminal. The given frequency of digital signal has high precision. As the frequency given is operated by switch contacts, it has strong capacity of resisting disturbance, is not easy to damage and is easy to maintain.
Communication given
The frequency given is completed by computer, PLC or DCS through communication interface.
Frequency given signal of VFD is roughly the several ways described above, and the ways to be used is selected through setting the VFD.
VFD was originally used to adjust the rotation speed of motor, but now it has been widely used in the process control of liquid level, flow rate, pressure and so on, and has become a new regulating mode.
VFD can be used as either the execution unit or control unit in the process control. When it’s used as an execution unit, the VFD receives control signal of control instrument to change the frequency of output power supply. When it’s used as a control unit, the VFD completes control task independently with its PID function. The above functions are to adjust the rotation speed of motor by changing the frequency of the motor power supply, so as to achieve the purpose of changing the controlled parameters.
In traditional control system, variable frequency is introduced to change the original control mode, to make the operation more stable and reliable while improving the system control precision. Compared with the traditional control system, VFD has replaced the control and execution unit, but their physical positions and control modes are different. At present, there are still disputes on the division of labor and the scope of duty.
Strictly speaking, VFD is an electrical control device. As it has a variety of control signal input mode and can be easily combined with the automatic control instrument to form a new control system, it has a promise application prospects in process control.
Panel Given Mode
It means to complete frequency given through the keyboard or potentiometer on the VFD operation panel. The VFD output frequency can be setting through up and down keys on the panel keyboard. Some VFDs are also equipped with a potentiometer, which can be rotated to set the frequency. Such a setting mode is suitable for local operation, which is convenient and easy, but it’s unable to transmit in a long distance.
External Given Mode
In this mode, the frequency given signal is input from the external terminal of VFD to control the output frequency. Common modes include:
1. Analog signal setting
It means to connect DC voltage or current signal from the VFD control terminal to complete frequency given, namely adjusting the VFD output frequency by changing the signal through dcs system, plc, PID regulator and manual operator. Commonly used voltage signals include: 0-10V, 2-10V, 0-±10V, 0-5V, 1-5V, 0-±5V. Current signals include: 0-20mA, 4-20mA. Current signal should be preferentially selected for this kind of signal because current signal has a long transmission distance and strong capacity of resisting disturbance. If the transmission distance is not long, the voltage signal can be selected.
2. Digital signal setting
It means to complete frequency given by inputting on and off signals through the VFD control terminal. The given frequency of digital signal has high precision. As the frequency given is operated by switch contacts, it has strong capacity of resisting disturbance, is not easy to damage and is easy to maintain.
Communication given
The frequency given is completed by computer, PLC or DCS through communication interface.
Frequency given signal of VFD is roughly the several ways described above, and the ways to be used is selected through setting the VFD.
VFD was originally used to adjust the rotation speed of motor, but now it has been widely used in the process control of liquid level, flow rate, pressure and so on, and has become a new regulating mode.
VFD can be used as either the execution unit or control unit in the process control. When it’s used as an execution unit, the VFD receives control signal of control instrument to change the frequency of output power supply. When it’s used as a control unit, the VFD completes control task independently with its PID function. The above functions are to adjust the rotation speed of motor by changing the frequency of the motor power supply, so as to achieve the purpose of changing the controlled parameters.
In traditional control system, variable frequency is introduced to change the original control mode, to make the operation more stable and reliable while improving the system control precision. Compared with the traditional control system, VFD has replaced the control and execution unit, but their physical positions and control modes are different. At present, there are still disputes on the division of labor and the scope of duty.
Strictly speaking, VFD is an electrical control device. As it has a variety of control signal input mode and can be easily combined with the automatic control instrument to form a new control system, it has a promise application prospects in process control.
Post a Comment:
You may also like:
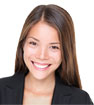
Variable Frequency Drives

Featured Articles
What is a Variable Frequency Drive
Variable frequency drive (VFD) is an adjustable speed drive used for motor drive system, control the speed and torque of the AC ...
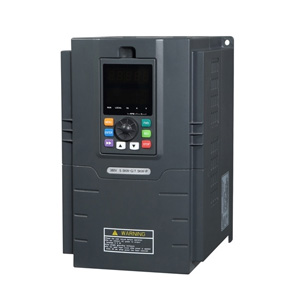